据储能界了解到,
本文亮点:1、对实际调峰工况下的电池进行液冷研究;2、采用调节冷却液流向和增大流量的方式优化液冷,提高冷却的均温性并设置最优流量区间;3、采用最大温度与平均温度的差值来评判均温性是否提高
摘 要 调峰是电池储能电站重要运行的工况,电池冷却对储能电站电池安全运行至关重要,本文对磷酸铁锂电池组在调峰工况下的液冷技术进行研究。首先对磷酸铁锂电池组在实际调峰工况下的产热以及电池的液冷冷却进行研究,建立磷酸铁锂电池组在调峰工况下的产热模型以及液冷冷却模型,其次对磷酸铁锂电池组在调峰工况下的液冷模型进行优化,通过有限元仿真分析,最后,采用调节冷却液流向以及合理调节流量等方式对液冷冷却进行优化。仿真与实验结果表明:合理设置不同冷却管冷却液流向可有效提高液冷散热的均温性,通过仿真温度云图的对比并创新地采用图片 (最大温度与平均温度的差值)来体现不同方案均温性的优劣;增大流量虽然有助于降温,但液冷倍率达到2.0以上时,冷却效果增加有限,但能耗大大增加,通过仿真结果提出最佳的流量范围为1.5~2.0。本文所提方案均已通过实验验证,并在储能电站电池冷却进行实际应用。
关键词 锂离子电池;调峰;液冷;有限元仿真
随着国家“双碳”战略和以新能源为主体的新型电力系统建设不断推进,以风电、光伏为代表的新能源接入给电网带来了巨大的压力,电化学储能是缓解电力-电量平衡矛盾的重要措施。锂离子电池具有比能量/密度高、循环寿命长等优点,成为电网储能电站的首选。当前,锂离子电池产业处于飞速发展阶段,据国家工信部报告,2022年全国锂离子电池产量超过750 GWh,同比增长130%。然而,作为一种极其复杂的电化学系统,锂离子电池仍然面临着显著的安全问题[6],特别是近年来因锂离子电池故障而引发的起火事件频频发生。缺乏良好的冷却设施是导致电池起火事故的主要原因之一,因此,本文对电网调峰模式下电站储能电池液冷冷却进行研究,并对目前储能电站冷却方式进行优化。
目前,储能电站液冷散热通过较强的热交换对电池进行快速降温,是国内外学者关注的焦点。Bernardi等学者基于能量守恒的基本原理,对电池进行热力学计算,得到了目前广泛应用的电池模型。
在电池液冷方面,孙广强等学者设计了一种冷却固定一体化冷板,采用数值模拟方法探究了冷却液入口流量、环境温度和冷却固定孔深度等参数对一体化冷板冷却性能的影响,并与蜂窝状冷板进行了性能比较。元佳宇等学者设计了具有单向流通结构和双向对流结构的蛇形管路电池组热管理系统。Mousavi Sepehrd等学者提出了一种结合相变材料(PCM)和液体冷却的新型混合冷却系统,以实现方形电池包的高性能和安全性。但是,当前文献对实际电池参与调峰的产热情况研究较少,特别是对设置不同冷却管冷却液流向模式、最优流量调节策略等均缺少研究。
在电池参与调峰方面,谭增强等学者分析了煤电机组调峰调频技术的现状,对调峰下电池产热进行了分析。Xue等学者开发分析了一种基于热泵-有机朗肯循环(HP-ORC)的新型调峰的储能系统,并通过温度对电池产热进行了分析。林海等学者对储能调峰电力系统优化做了研究,研究了调峰的储能电池的产热模型。文献[12-14]都是考虑了储能电池参与调峰调频实际工况时的产热,提出了调峰模式下电池的产热模型,但由于受文章篇幅限制,缺乏对于如何进行冷却来控制温度的考虑。
因此,本文对实际调峰工况下电池的产热方式进行研究,对产热的模型进行液冷冷却仿真分析,通过建立电池组冷却结构模型,对其进行分析并提出优化方案,提出冷却液交叉式流入策略以及流量调节策略。本文研究对调峰工况下提高电池组的使用性能和寿命具有重要的现实意义。
1 电池热特性及液冷热传导分析
热特性研究是冷却技术研究的基础,本节首先对调峰工况下的储能电池产热特性进行分析。
电池应用于电网高峰运行时,进行多次充放电,电池内部会发生氧化还原反应产生热量。磷酸铁电池的放热主要包括反应热、焦耳热、极化热以及副反应热,产热的表达式为:
2 储能电池产热和散热仿真分析
以磷酸铁锂电池为研究对象,其正极材料为磷酸铁锂,负极材料为石墨。磷酸铁锂电池储能技术在新能源高效消纳、电力系统灵活调节方面具有独特优势,与三元锂电池相比,磷酸铁锂较好的安全性使其在储能领域更具有应用前景。
采用Comsol进行冷却研究,Comsol是一款大型的高级数值仿真软件。广泛应用于各个领域的科学研究以及工程计算,模拟科学和工程领域的各种物理过程。Comsol是以有限元法为基础,通过求解偏微分方程(单场)或偏微分方程组(多场)来实现真实物理现象的仿真,本文根据储能电池的实际调峰工况搭建模型,并进行仿真计算分析,分别在调峰工况下对底部液冷和侧边液冷进行分析并得出相关结论。
2.1 仿真边界条件
用Comsol软件对电池冷却进行仿真分析时对储能电池冷却系统作出以下几点假设:①固液之间无相对滑动;②忽略流体惯性力以及边界压力差为0;③忽略冷却系统的结构变形;④在考虑电池产热时只考虑占比最大的焦耳热,忽略其他三种热。
在瞬态求解计算时采用湍流模型进行计算,周边的冷却管内为流体区域,电池设为固体区域,流体固体的接触面为流固耦合的传热边界,环境温度为25 ℃。
如表1所示为本文仿真分析所用电池的实际参数,以电池工作电压为2.7~3.8 V,单体电量220 Ah,充电最大电流为110 A,电池簇为8块电池串联,电池与电池之间有6 mm的间距。仿真电池的数据与实际电池数据相一致。
表1 仿真与实测用电池簇参数
2.2 仿真中实际调峰工况
25 ℃时电池调峰工况110 A恒充恒放曲线如图1所示。将实际工况的电流作为仿真输入,后续对仿真中的电池进行温度的分析。
图1 现场工况下的电流曲线
2.3 仿真研究
2.3.1 调峰工况仿真产热研究
电池仿真产热几何模型如图2所示。
图2 电池产热几何模型图
仿真前要先进行网格剖分,采用自由四面体网格对电池极柱进行网格剖分,采用自由三角形网格对电池表面进行剖分,仿真软件自动构建网格网络,网格剖分结果如图2所示。
将实际调峰工况下的电流数据输入到仿真模型当中,电池在调峰工况下110 A恒充恒放时电池产热的结果如图3所示。热仿真步骤如下:①将实际调峰工况波形作为模型输入,以公式(7)传热方程来实现电池传热,电导率理论选择电流接口;②塞贝克系数理论研究选择电流、固体传热以及电化学热进行多物理量耦合;③网格剖分后进行仿真计算。
图3 电池产热模型温度分布图
电池最高温度可以达到36.8 ℃,长时间工作在此温度下对电池寿命有较大影响,因此需要对电池进行冷却。系统采用底部液冷和侧边液冷的方式,液冷板结构如图4所示,下面基于此分别观察电池组在不同液冷方式下温度下降的程度以及整体均温性的效果。
图4 液冷板结构图
2.3.2 液冷冷却位置
磷酸铁锂电池组目前主流的冷却方案为底部冷却和侧面冷却,在0.5 C的平均充电倍率下对电池组进行液冷冷却仿真(冷却液的基准流量为10 L/min,对应的入口处冷却液流速为0.1 m/s),在调峰工况下液冷仿真的温度分布如图5(a)、5(b)所示,为便于下面对比分析,本文称之为冷却方案一与冷却方案二。
图5 25 ℃下调峰液冷温度分布图
冷却方案一:冷却液从图所示的底部方向流入流出,经过一定换热,底部与产热较多的极耳处存在一定的温差。所以,整体温控趋势为下部温度低上部温度高,进口温度低出口温度高。底部液冷可以将电池最高温度控制在27.2 ℃以下,整体降温达到了9.6 ℃,从降温总量看,达到降温的目的;但整体温差为2.2 ℃,整体温度分布不够均匀。
冷却方案二:冷却液从图5(b)示侧边方向流入流出(为了图例更加清楚只画出一侧的冷却液流向),经过一定换热,可以看出,入口处换热效果是优于出口处的效果。主要的冷却位置为两侧边,与方案一对比,方案二无论是的降温总量还是均均温性均好于方案一。本文仿真的调峰工况下侧边液冷可将最高温度控制在26.5 ℃以下,整体的温差控制在1.5 ℃左右。
最高与最低温度差不能说明电池整体均温性的效果(一般最低温度为冷却液进口温度,人们关心的重点不是进口最低温度,而是电池的最高温度),为了对电池散热均温性进行量化分析,定义图片为电池的平均温度与最高温度的差值,作为电池均温性是否提高的评判标准(电池平均温度已在图中用红点标出)。冷却方案一的图片为1.4 ℃,冷却方案二的图片为0.9 ℃。
2.4 液冷仿真优化
2.4.1 调节冷却液流入方向优化液冷
本文中,冷却方案一和二都将电池的温度控制在28 ℃以下,此时,冷却的均温性对电池寿命影响更大,所以本文先采用调节冷却液流向的方式优化液冷散热的均温性。
对冷却方案一,不但要考虑均温性,还有考虑降温效果,优化结果如图6所示(冷却方案三)。冷却方案三在底部液冷中交叉设置流入流出口,最高温度控制在27.7 ℃以下,而图片控制在0.7 ℃,方案三的均温性相较于方案一提高较多,但降温总量上表现较差,最高温度相对原来方案一甚至略有上升。
图6 底部液冷异侧流入的温度分布图
交叉式流入的方式对提高均温性的效果体现在电池的图片中,由于方案三相较于方案一的图片明显下降,均温性明显提高。因此,选用方案一与方案三的温度对比图来验证均温性是否提高。如图7所示为底部液冷冷却方式在调整冷却液流向前后的电池温度曲线对比图。
图7 调整冷却液流入方向前后的温度曲线对比图
图7(a)为冷却方案一的温度曲线图,图7(b)为冷却方案三的温度曲线图,蓝色线表示电池组运行时的最高温度,红色线表示电池运行时的平均温度,绿色线表示电池运行时的最低温度,从图中可以看出,对于冷却液交叉流入方式,虽然整体温度都上升,但图片从1.5 ℃降低到0.7 ℃(如图中AB点的温差与CD的点温差),温差降低,均温性提高。但降温效果仍有不足,需要采取其他方式进一步优化方案一的降温效果。
上述方案二在降温效果方面已基本达到要求,但图片仍较大,均温性还有优化的空间。首先对方案二进行优化,先取三种有代表性的流入方向来优化冷却。如图8所示为侧边液冷改变流入方向的温度分布图(为图例表达清楚只画出了部分流入流出方向)。
图8 侧边液冷改变流入方向的温度分布图
冷却方案四如图8(a)所示,冷却液两侧流向相反,可以将最高温度控制在26.7 ℃以下,同时也能提高整个电池组的均温性,图片为0.7 ℃。
冷却方案五如图8(b)所示,每侧8个冷液进出口分为两组,不但对侧流向相反,而且上下两组流向也相反。这种方案的仿真结果整体可以将最高温度控制在26.6 ℃以下,通过这种优化方式,可以做到降低温度的同时也能提高电池整体的均温性,图片为0.5 ℃。
冷却方案六如图8(c)所示,将冷却流入方式由多管同向流入改为每个相邻管均反向流入,即冷却液进出口间隔设置流入与流出(交叉流入方式)。仿真结果表明,交叉流入方式,图片为0.4 ℃,并且温度云图显示整体温度最均匀。
在方案四~方案六中,最高温度与最低温度之间的差值比方案二大,但图片较小,电池温度云图的温度分布更均匀,大部分电池均温性上升,可能存在小部分电池均温性较差,但整体均温性仍然是提高的,可见文献[17]。
2.4.2 增大流量优化液冷
对于通过上述改变冷却液流向的优化方案,虽然温差大大减小,均温性得到明显提升,但电池组降温总量不明显,甚至有的方案最高温度还略有上升,此时对于电池寿命的主要影响因素变为电池的最高温度,因此,进一步采用增大流量的方式优化降温效果。如图9为通过增大入口处冷却液流量来优化液冷的温度分布,将流入口的流量分别增大为原来流量的2倍和3倍,可以看到,增大入口处的流量对于控制温度有显著的作用(基准流量时的电池温度分布见图5),但是流量进一步增大,对降温的提升效果不明显,并且在工程实际当中,增大流量会增加冷却成本,因此,采取合理的流量增大策略在工程应用中至关重要。
图9 液冷增大流量的温度分布图
增大冷却液流量的倍率与电池最高温度的关系如图10所示,可以看出,底部液冷的冷却液流量倍率增大到2.0左右时,侧边液冷的冷却液流量倍率增大到1.5左右时,电池温度变化减缓(低于仿真的测量分辨率),这时进一步增大流量温度下降有限,但冷却成本增加。实际工程中底部液冷可以将流入口的流量倍率控制在1.5~2.0倍,而侧边液冷可以将流入口倍率控制在1.5倍左右即可。
图10 液冷倍率与最终温度的关系曲线
2.4.3 液冷优化结果
如表2所示,通过调整冷却液流入方向和调节冷却液流量两种不同方法对液冷进行相应的优化。调整冷却液流入方向侧重点是增强电池整体的均温性,可以看到相较于方案一方案二,流入方向由同侧流入改为异侧交叉流入后图片都有所下降,证明改变流入方向的优化方式的有效性;增大冷却液流量侧重于电池的温度控制,制定合理的流量调节策略可以实现降温总量与经济性的双效最优。
表2 液冷优化方式总结
因此,综合考虑降温效果与均温性后,最终冷却优化方案为,侧边液冷采用方案五,并将流量倍率增加到1.5倍,底部液冷采用方案三,将流量倍率增加到2.0倍。最终的冷却效果如图11所示。
图11 侧边液冷与底部液冷最终方案温度分布图
通过改变侧边液冷的冷却液方向可以很好地提高电池冷却的均温性,同时,在该方案下[图11(a)所示],可以采用较低的冷却液增大倍率即可达到较好地温度控制效果,底部液冷最终方案[图11(b)]通过改变冷却液流向和流量倍率也可达到温度控制的目的,实际工程中出于经济性的考虑,可使用优化后的底部液冷,对温度较高的电池组使用侧边液冷,以达到冷却效果与经济效益的综合最优。
3 储能电池实验分析
3.1 实验平台
实验平台如图12(a)所示,由上位机、具有双通道的宁波拜特BT60V300AC2电池测试系统等组成,每个电池设置温度传感器。电池处于恒温箱中,通过上位机设置每一工步具体参数,调节策略参照镇江某储能电站的电网调峰实际工况,包括调峰电流,静置时间等,对储能电池组产热方式进行实验验证,最终利用上位机监控电池温度、电流电压等参数。
图12 实验平台
液冷散热实验系统如图12(b)所示,每一个单元格内对电池进行底部液冷,通过温度传感器记录温度变化,传递到上位机读取温度读数。
3.2 实验结果与仿真结果对比
电池在模拟电网调峰模式下产热状态的温度仿真与实验对比曲线如图13所示。由图13可以看出仿真温度与实际温度的差值都在1 ℃之内,达到误差标准,实验验证了仿真模型的正确性。由于现场温度传感器安装位置在电池的极耳处,也就是发热最严重的地方,所以产生温度会比仿真温度略高。
图13 电池产热的温度实验与仿真对比曲线
电池在模拟电网调峰模式下底部液冷(方案一)的温度仿真与实验对比曲线如图14所示。图14的工况相较于图13略有改变,充放电中间添加了1 h的静置时间(停止充放电1 h),图14的波动是因为这种工况下,充放电结束后会静置1 h,此时,液冷单元仍在工作,温度会下降,而静置结束后,电池组重新开始充放电,温度又会再次上升,所以温度存在一定波动。通过实验数据与仿真数据的对比,电池最终冷却温度为27.2 ℃与实验数据27 ℃差值在1 ℃之内,可以验证电池底部液冷散热仿真模型的准确性。
图14 电池底部液冷的温度实验与仿真对比曲线
4 结 论
本文对储能电站电池组在实际调峰工况环境下产热与冷却进行仿真与实验分析研究,得出以下三点结论:
(1)建立了储能电池在实际调峰工况下的产热模型,采用仿真温度与实验温度对比的方式验证了产热模型的正确性。仿真与实测结果表明,25 ℃的室温中,储能电池的最高温度达到36.8 ℃。
(2)对液冷优化方面,采用了调节冷却液流向和增大流量的方式来优化液冷冷却的效果:冷却液交叉流入方式可以一定程度上提高冷却的均温性;增大流量对降温有较好的效果,但增大到一定倍率后降温效果不明显。一般流量增大倍率在1.5~2.0之间为冷却效果与经济性均较好,工程实际中可根据现场情况进行参考,选择合适的方式进行液冷优化。
(3)储能电池调峰工况下底部液冷方式,降温效果虽可达到要求,但是整体温差较大;侧边液冷方式不仅降温效果好,均温性也达到要求,但成本较高。实际工程一般情况下可使用优化后的底部液冷,对温度较高的电池组使用侧边液冷,以达到冷却效果与经济效益的综合最优。
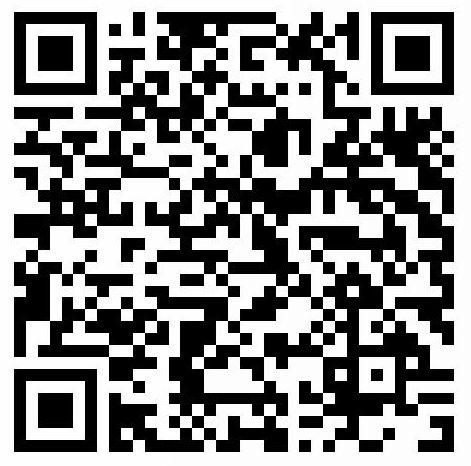
评论