据储能界了解到,
摘要:锂离子电池电极微观结构对电极活性物质的电化学性能有着重要的影响。利用双层涂布技术实现了不同组成、不同孔隙结构的双层磷酸铁锂电极构筑,其中通过在远离集流体的电极涂层组分中添加碳酸氢铵,使得电极涂层从集流体到电极表面呈现出孔隙率逐渐增大的电极结构特征。结果表明,从集流体到电极表面呈现出孔隙率逐渐增大的双层结构厚电极(涂层厚度为77.3 μm),常温1 C倍率下放电比容量达145.3 mAh/g,60次循环后容量保持率为97.2%,常温5 C倍率下仍具有40 mAh/g的放电比容量,而相同面密度下单层结构厚电极(涂层厚度为74.9 μm)的5 C放电比容量为0。
关键词:锂离子电池;造孔剂;双层电极
随着新能源的高速发展,锂离子电池作为当前最常用的可充电电池之一,在移动设备、电动车等领域得到了广泛应用。电动汽车不断增长的需求加速了高能量密度电池的发展[1]。提高能量密度最有效的方法之一是制备厚电极,以提升活性材料占比从而降低非活性组分如集流体、隔膜以及电解液的比例[2]。但是随着极片厚度的增加,电极内部电子传输和离子扩散路径增长,导致电池的极化增加[3-4]。因此在电极配方优化的同时,也需要对电极结构进行优化,改善Li+传输动力缓慢的问题。
当前,研究采用外加磁场诱导法、3D打印法、无溶剂粉末挤压成型法、激光刻蚀技术 以及静电纺丝法等,在电极内部锂离子传输方向上构筑定向排列的微通道,来提升厚电极的电化学性能。Heubner等[5]发现降低孔隙率会增加欧姆阻抗和电荷转移阻抗,同时降低接触电阻和电解液中的有效离子扩散率。Yu等[6]利用树木的天然导管结构,制备了具有垂直微孔结构的超厚LiCO2电极,且木制LiCO2电极能提供高达22.7 mAh/cm2的高面容量。然而,这些方法难以产业化实施。与此同时,多层涂布技术也是构筑厚电极且能产业化的方法之一。Wang等[7]构建了上下层导电剂含量不同的双层结构电极,发现导电剂添加含量较低的顶层有着更高的孔隙率,同时在相同的电流密度下活性材料负载高的双层比活性负载低的单层电极电化学性能更优。Song等[8]通过静电纺丝和刮刀涂布法制备了不同孔隙率的双层电极,其底层使用刮刀表层使用静电纺丝的方法制备的孔隙率梯队变化的电极,在0.5 C倍率下具有150 mAh/g的放电比容量。尽管如此,双层结构厚电极依然存在离子扩散路径增长的问题。
基于此,本研究通过两次涂布的方法构筑双层结构厚电极,并在电极浆料中加入造孔剂,进而在双层厚电极中实现垂直孔道结构,然后对比了双层厚电极与单层厚电极间的电化学性能。
1 实验
1.1 电极片制备
将磷酸铁锂(LFP)、导电剂炭黑(SP)加进聚偏氟乙烯(PVDF)的N-甲基吡咯烷酮(NMP)溶液中(其中LFP、SP和PVDF的质量比见表1),用磁力搅拌器以1 000 r/min搅拌3 h形成均匀的浆料。使用四面制备器将浆料涂敷在16 μm铝箔集流体上,在80 ℃下烘干后,将辊压的极片冲压成直径12 mm的电极片,再在80 ℃下真空烘干,制备出五种不同组成的单层薄电极,分别标记为P1、P2、P3、P4和P5。
表1 用于磷酸铁锂电极配方筛选的单层薄电极工艺参数
为了获得不同孔隙率的双层电极,将LFP、SP和PVDF按照表2中的质量比称量混合后,用磁力搅拌器以1 000 r/min搅拌3 h形成均匀的浆料,再通过刮涂(四面制备器)的方式制备出三种厚电极(图1)。其中,S1为浆料A经单次涂覆而获得的单层结构电极,通过80 ℃烘箱干燥12 h;D1为浆料A经两次涂覆而获得的双层结构电极,第一次在集流体上涂覆浆料A,然后在80 ℃烘箱干燥40 min得到电极底层涂层,之后再将浆料A涂覆在底层上,然后干燥12 h;D2为先后两次涂覆浆料A和B获得的双层结构电极,第一次在集流体上涂覆浆料A,然后在80 ℃烘箱干燥40 min得到电极底层涂层,之后通过四面制备器将浆料B涂覆在底层上,然后干燥12 h。将烘干后的三种电极辊压至设定压实密度后,再冲压出直径12 mm的电极片,其参数如表3所示。
表2 用于制备双层电极的磷酸铁锂单层配方组成 g
表3 不同配方的磷酸铁锂厚电极工艺参数
1.2 分析方法
在充满氩气的手套箱中将制备好的电极片组装成CR2016型纽扣电池,制备的电极片作为正极,锂金属作为负极,电解液为1 mol/L LiPF6[碳酸乙烯酯(EC)+碳酸甲乙酯(EMC)+碳酸二乙酯(DEC),质量比为3∶5.5∶1.5],组装电池时使电解液充分浸润隔膜和电极片,手套箱水分和氧气含量控制在10-7以下。
采用Hitachi SU8010型扫描电子显微镜(SEM)(日本产)分析电极材料表面形貌。采用STA 449 F5型X射线能谱仪(德国Netzsch公司)分析电极的表面元素组成。
使用BTER1300极片电阻仪(元能科技)分析极片的电阻率,测试压强范围为5~60 MPa,压强步进为4 MPa。使用Neware5V10mA电池测试柜对组装后的电池进行恒流充放电测试,电压窗口为2.8~4.2 V,电流密度为170 mA/g (1 C),所有测试均在25 ℃室温条件下进行的。采用电化学工作站(Echemlab HV,英国Solartron analytical)测量电化学阻抗谱(EIS),频率范围为0.02~10 kHz,振幅为10 mV。使用全自动压汞法孔径分析仪(MicroActive AutoPore V 9600 Version)对极片进行孔隙分析,进汞接触角为130,汞的温度为25.53 ℃。
图1 S1、D1和D2三种厚电极结构示意图
2 结果与讨论
2.1 磷酸铁锂电极组成对电化学性能的影响
电极中粘结剂PVDF是将电极材料粘结在一起的物质,不导电且不提供容量,而导电剂则是帮助电子在电极中传输的物质。图2(a)给出了不同压实密度下极片电阻率的变化情况,可见,P2、P3和P4相比,极片中粘结剂含量保持在5%,导电剂SP含量从10%降到2%,其极片初始电阻率从P2的678.1 Ω·cm增加到P4的9 864.2 Ω·cm;P1、P3和P5相比,极片中导电剂含量保持在5%,粘结剂PVDF含量从10%降到2%,其极片初始电阻率从P1的2 012.1 Ω·cm增加到P5的10 487.5 Ω·cm。这说明电极中过低的粘结剂含量或过低的导电剂含量都会导致电极片电阻率的增大,P2电极的电阻率最低。此外,随着电极压实密度的增加,电极材料间接触电阻变小,电极的电阻率也会随之下降。
为了研究五种配比的电极在电荷传输动力学方面的差异,将电极片组装电池静置12 h后进行EIS分析。如图2(b)所示,P1、P2、P3、P4和P5的电荷转移阻抗(Rct)分别为173.7、80.6、107.8、366.6和139.8 Ω,P2电极的Rct是最低的。此外,对比P2、P3和P4的Rct值能够看出,随着导电剂含量降低,电极的Rct在增加;同时从P1、P3和P5中看出导电剂相同,降低粘结剂含量并提高LFP含量,粘结剂含量从10%降到5%时Rct从173.7 Ω下降到80.6 Ω,接着粘结剂含量从5%下降到2%时,Rct从80.6 Ω上升到139.8 Ω,说明适当减少粘结剂含量可以减小电池的Rct,但是当粘结剂含量下降到一定程度时,Rct反而增加。
图2 不同配方的磷酸铁锂薄电极电性能比较
图2(c)为5种配方薄电极电池的倍率性能,5种电池在室温0.2 C时P2比容量为156.1 mAh/g,在1 C、2 C和5 C时,P2电极的比容量分别下降到143.2、131.8和110.5 mAh/g,当电流密度回到0.2 C时,比容量恢复到158.5 mAh/g,高于其他组电池在相同倍率下的放电比容量。同时P4电池的电流密度增加到5 C时,电池比容量下降到接近0,说明当导电剂含量下降到2%时,电池已经不适合大电流放电。同时,在低电流密度下,相同导电剂含量电池放电比容量相差不大,如P1、P3和P5电池在0.2 C的比容量分别为143.4、147.7和146.88 mAh/g。但是随着电流密度逐渐增加,差异会逐渐增加,尤其当电流密度增加到5 C时,P1、P3和P5电池的放电比容量分别为81.1、100.7和85.6 mAh/g,P3组电池分别比P1和P5组电池放电比容量高出20%和17.6%,该结果与EIS及电阻率测试结果相吻合。也就是说,合适的电极配方是要兼顾到电极的电子导电性和电极材料间的接触阻抗间的平衡。
图2(d)为5种电池室温下1 C倍率的60次循环性能比较,从图2(d)中能够看出P2电极在循环60次时有着最高的放电比容量149.7 mAh/g。而P4电池的容量从循环开始时就快速下降,在20次以后放电比容量已经衰减到接近0,说明较低的导电剂含量电极的循环性能较差。同时比较P1、P3和P5电池的长循环,发现较高的粘结剂含量和较低的粘结剂含量都不适合电池的长循环。
综合分析来看,LFP、SP和PVDF质量比为85∶10∶5的电极配方性能最佳,尽管这种配比缺少实际的产业化应用潜力,但结果对产业化配方设计工作有指导意义。基于此,接下来的厚电极工作在LFP、SP和PVDF质量比为85∶10∶5的电极配方上开展。
2.2 双层电极结构对电化学性能的影响
图3是S1、D1和D2电极涂层的SEM截面和表面形貌照片,其中图3(a)~(c)分别为S1、D1和D2电极的截面照片,(d)~(f)分别是S1、D1和D2电极的表面形貌照片。可见,S1、D1和D2等3种厚电极的辊压后涂层分别为74.9、77.7和77.3 μm,厚度相当且双层电极与层电极结构基本相同,没有产生明显的分层边界。此外,3种电极的厚度均高于配方筛选所用电极厚度,成功构筑了较厚电极。用应用程序ImageJ模拟和计算不同电极的表面孔隙率,表明远离集流体的表层浆料加入造孔剂的D2电极表层孔隙率为26.5%,高于S1(19.1%)和D1(21.1%)孔隙率,压汞实验结果也证明了这一趋势(图4)。
图3 S1、D1和D2电极片的截面图(a)~(c)、电极表面形貌图(d)~(f)和表面孔分布模拟图(g)~(i)
图4 压汞实验中S1、D1和D2电极片不同压力下进汞量
图5 S1、D1和D2电极片压实密度与电阻率间关系
图5是S1、D1和D2三种电极片压实密度与电阻率之间的关系。S1电极的在5 MPa下的压实密度为1.51 g/cm3,D1和D2电极在5 MPa下的压实密度分别为1.481和1.37 g/cm3。三种电极的初始压实密度相差不大,但从初始电阻率能够看出双层电极D1的电阻率(101.6 Ω·cm)和D2的电阻率(74.9 Ω·cm)均比单层电极S1的电阻率(390.7 Ω·cm)小,三种电极的压实密度与电阻率趋势都是相同的,极片的电阻率都是随着压实密度的增加而降低。此处采用与前面单层薄电极相同的压实密度(1.84 g/cm3)进行后续实验。
图6 S1、D1和D2电极半电池常温第一次充放电循环前后交流阻抗(a-b),倍率性能(c),长循环性能(d)
对比P2与S1的EIS数据(图2和图6),可以发现,相同的配方下极片涂层厚度从29 μm增加到74.9 μm,交流阻抗中Rct从80.6 Ω增加到112.8 Ω,两种极片电池在常温0.2 C的倍率下放电比容量分别为156.1和144.49 mAh/g,在1 C的倍率下两种电池常温循环60次后放电比容量分别为149.7和118.3 mAh/g,表明常规电极涂层厚度增加会导致电极电化学性能降低。
对比P2与D2的EIS数据(图2和图6),可以发现,具有梯度孔隙电极涂层厚度为77.3 μm,其电池交流阻抗Rct为78.8 Ω,与相同配方的单层薄电极的Rct值相当。常温0.2 C倍率下P2与D2电池的放电比容量分别为156.1和159.13 mAh/g,在1 C下两种电池常温循环60次后放电比容量分别为149.7和141.2 mAh/g。D2电极相对于P2电极涂层厚度增加了2.7倍,但由于D2电极片的双层多孔结构,电极更容易被电解液浸润,提高了D2电极的电化学性能,使得D2厚电极与P2薄电极电化学性能相当。
此外,从图6可以看出,S1、D1和D2电极组装成纽扣电池的初始Rct分别为139.6、112.8和78.8 Ω,常温1 C循环60次后的Rct分别为239.0、276.9和382.9 Ω,说明表层较大的孔隙率的电极结构有利于电极电化学性能的发挥。
图6(c)展示了S1、D1和D2三种电极制备电池的倍率性能。可以看出,在常温0.2 C倍率下,三种电池的放电比容量分别为144.49、155.9和159.13 mAh/g。但是随着电流密度的逐渐增加差异会逐渐增加,尤其当电流密度增加到5 C时三种电池的放电比容量分别为0、0和44.5 mAh/g,说明表层有着更高孔隙率的厚电极更适合高电流密度放电,该结果与EIS及电阻率测试结果相吻合。
除了电池的倍率性能外,循环稳定性同样重要。图6(d)呈现了S1、D1和D2电极的循环性能。S1、D1和D2在常温1 C倍率下初始放电比容量分别为131.5、140.5和145.3 mAh/g。经历60次循环以后放电比容量分别为118.3、136.0和141.2 mAh/g,容量保持率分别为89.7%、96.7%和97.2%,表明表层具有更高孔隙率的电极,不仅有着更高的放电比容量,而且电极的循环稳定性与容量保持率也有所提升。
图7 S1、D1和D2三种电极片辊压后的电镜照片(a)~(c)和1 C循环60次后极片电镜照片(d)~(f)
图7给出了S1、D1和D2三种极片辊压后和常温1 C循环60次后的电极片电镜照片。可见,3种厚电极的新极片表面均是光滑无裂纹,但是循环后的厚电极片表层均出现裂纹,相比而言,表层有着较高孔隙率的D2双层电极,表层裂纹最少。说明从集流体到电极表面呈现出孔隙率逐渐增大的电极结构特征,可以降低厚电极的开裂风险,从而提升厚电极电池的电化学性能。
图8给出了S1、D1和D2三种厚电极片电池的常温0.2 C首次充放电曲线,其充放电曲线的中值电压差分别为0.17、0.14和0.1 V,表明D2电极的极化小于D1和S1电极,进一步证明了表层孔隙率更高的电极有着更加优异的电化学性能。
图8 S1、D1和D2三种厚电极片电池的常温0.2 C首次充放电曲线
最后,为了验证造孔剂在极片烘干以后没有造成残留,对烘干的极片分别使用X射线衍射(XRD)和X射线光电能谱(XPS)进行分析。如图9(a)所示,烘干以后的D2电极片中不含NH4HCO3的特征峰,说明D2极片烘干后没有NH4HCO3残留。同时如图9(b)所示,XPS图谱半定量分析结果表明,氮的质量含量约为碳含量的0.1%,表明NH4HCO3在电极中残留量可以忽略不计。
图9 干燥后D2电极的XRD图谱(a)和XPS能谱(b)
3 总结
电极是电池中的重要部分,是将化学能转化为电能的地方,其性能由电极电子电导率和离子电导率综合决定。粘结剂PVDF因为不导电的缘故,在电极中含量高会提升电极材料间的粘结力,但会降低电极的电子电导率;高含量导电剂会增加电极的电子电导率,较大的比表面积需要更多粘结剂来粘结,所以电极中导电剂和粘结剂的含量需要适量。离子电导率由电极活性物质本身的离子电导率和电解液的电导率综合决定的。厚电极是提升电池能量密度的重要技术手段之一,但存在电解液浸润难电极性能差的问题。本研究以NH4HCO3作为造孔剂制备的不同孔隙率的双层电极,没有NH4HCO3残留,不会对电极成分产生影响。表层浆料加入造孔剂使电极表层有着更高的孔隙率,强化了电解液对电极的浸润能力,有效的提升了厚电极的电化学性能,在5 C的电流密度下,辊压后涂层厚度为77.3 m的D2电极放电比容量为44.6 mAh/g,与辊压后涂层厚度为29 m的单层电极性能相当;而辊压后涂层厚度为74.9 m的S1单层厚电极与不加造孔剂的D1双层厚电极,他们在5 C倍率下放电比容量为0。通过加入造孔剂改变电极的孔隙分布,可以提升电池的倍率性能以及电池的循环性能,该方法可以为高能量密度电池提供一种有效厚电极构筑策略。
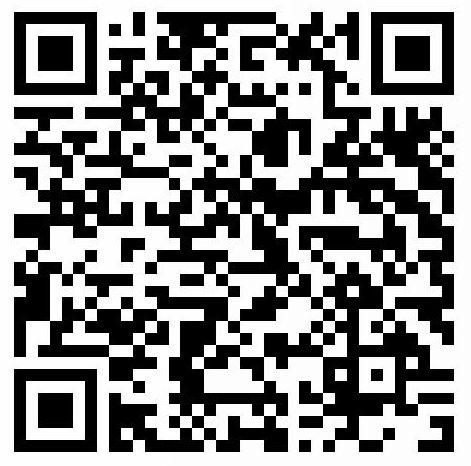
评论