据储能界了解到,
本文亮点:1. 设计了基于圆柱形相变单元的储热装置;2. 获得了储热装置内部的温度演化规律。
摘 要 水合盐相变储热技术具有储热密度高、成本低等优势,在清洁供暖中具有广阔应用前景。本研究设计并搭建了以三水合乙酸钠作为储热材料,以圆柱形相变材料封装单元作为基础单元的填充床相变储热装置。通过实验研究填充床储热装置的运行特性,研究了流量和储热温度对装置的储释热用时、出口温度、热效率及储热密度的影响。实验结果表明:提高储热温度和增大流量可缩短储热用时、提升热效率和储热密度。储热装置的热效率可达94.73%,储能密度可达71.77 kW·h/m3。
关键词 无机水合盐;相变材料;储热装置;填充床
储热技术可将太阳能、电能等以热能形式进行储存,具有技术成熟、寿命长等优点,在电力、建筑、工业等领域得到广泛应用。基于相变储热材料的储热技术为相变储热技术。相变材料在相变过程中以近似恒温的状态完成相变潜热的积累和释放,因此相变储热技术具有储能密度高、恒温放热等优点。在我国,冬季供暖能源需求季节性波动是构成能源供给、冬季大气质量以及环境保护较大压力的重要因素。为了构建清洁低碳的区域能源体系,北方地区正在积极提升太阳能、风能等可再生资源的占比,全面推进清洁能源供暖,并逐步将建筑能源领域的能源供应由煤炭、天然气等化石燃料向可再生能源转换。然而,可再生能源存在间歇性和不稳定性,导致其供应与需求常常在时间或空间上不一致,大量能源被弃用。相变储热技术可以以热能形式储存可再生能源,且满足建筑用热的恒温供热要求,是降低冬季供暖能耗的有效手段。目前,冬季供暖主要有散热器供暖、地板辐射供暖和空调设备供暖等几种形式。其中,地板辐射供暖相较于其他供暖形式,具有节能、人体热舒适性高等优点。中低温相变储热技术的供温范围一般在40~80 ℃ ,与供暖场景用热温度需求匹配度高。三水合乙酸钠作为无机水合盐中低温储热材料,凭借其相变潜热高、无毒、低腐蚀性、不可燃等优点在相变储热领域受到了广泛关注,其相变温度为58 ℃,与辐射供暖的用热温度相匹配。基于三水合乙酸钠的相变储热装置能够实现热能储存,并作为供暖热源,满足多变的供暖需求。
储热装置作为储热系统的核心部分,其种类较多,包括流化床、板式、板翅式、管壳式和填充床,不同类型的储热装置在储热性能上存在差异。其中,相变填充床以密闭单元封装相变材料,形成堆积结构,具有结构紧凑、换热效率高等优势。在针对中低温储热填充床运行特性的研究中,目前研究者普遍采用球形封装单元,而封装材料则主要包括塑料和不锈钢。实践证明,在相同运行条件下,基于球形封装单元的相变填充床储热装置较纯水箱存储更多的储热量。以钱怡洁和何兆禹的研究为例,他们设计了一台容积为0.75 m3,理论储热量为100.57 MJ的相变储热水箱(储热材料:石蜡;相变温度:67~69 ℃),比较相同运行条件下(0.3 m3/h,释热截止温度67 ℃)的储热量,相变储热水箱比纯水箱多释放15.55 MJ,相当于传统水箱理论储热量的15.5%。此外,封装单元尺寸、流量、储热温度等因素也被证实会影响填充床的储热性能。Regin的研究表明,当球形封装单元直径从60 mm缩小至30 mm,装置储热用时从630 min减少至480 min,减少23.8%。王峰等则研究了流量对储热装置(储热材料:石蜡;封装单元材质:聚丙烯;壁厚:1.0~1.5 mm)的影响。其结果表明,增大流量可缩短储热和释热用时,当流量从0.1 m3/h提升至0.3 m3/h,储热用时减少46%,释热用时减少43.4%。Kumar研究了储热温度对储热装置(储热材料:相变材料OM48;相变温度区间:45~50 ℃)储热用时的影响。结果显示,提升储热温度可以缩短装置储热用时。当储热温度从60 ℃提升至80 ℃,储热用时从153 min缩减至108 min,减少了29.4%。
相较于球形单元,圆柱形单元排布可以实现更高的堆积密度,具有较高的应用潜力。然而,目前基于圆柱形相变单元储热装置的储释热特性研究还相对较少。因此本文设计并研发了采用圆柱形相变单元作为材料封装单元的填充床,建立了储释热实验系统,研究了各种参数对水合盐填充床储释热特性的影响。本论文其余部分设置如下:第1节介绍了填充床储释热特性实验研究所涉及的实验装置、实验系统、实验步骤和研究内容;第2节我们获得了填充床内部温度演化情况,并进一步研究了储热温度和运行流量对填充床储热性能的影响;第3节,对研究结果进行总结归纳,并整理成结论。
1 填充床储释热特性的实验研究
1.1 实验装置
本研究所用圆柱形相变单元,材质为304不锈钢,密封方式为端侧螺纹密封。图1(a)为封装单元外形示意图。封装单元总长为390 mm,相变单元主体外径为32 mm,相变单元壁厚为1.7 mm。部分相变单元内部含有热电偶温度测点,测点位置为单元几何中心。
图1 相变材料封装单元及填充床储热装置示意图:(a) 相变材料封装单元;(b) 填充床储热装置三维示意图;(c) 填充床储热装置结构示意图
三水合乙酸钠主要存在高过冷度和相分离两个缺点。过冷现象是指相变材料降温至相变点以下仍保持液态而不发生结晶。三水合乙酸钠在不添加成核剂的情况下过冷度最高可达88 ℃。相分离是指水合盐熔化过程中生成的盐无法全部溶解于其生成的水中,导致固体盐沉降至底部。相分离造成熔融体系均匀性降低,水合盐结晶能力降低。为改善其缺陷,本研究采用十二水合磷酸氢二钠和羧甲基纤维素钠分别作为成核剂和增稠剂,以改善三水合乙酸钠的过冷度和相分离。我们通过熔融搅拌法制备了三水合乙酸钠、十二水合磷酸氢二钠和羧甲基纤维素钠按98∶1∶1质量比混合的复合相变材料。此配比下复合相变材料的相变潜热为268.4 J/g,相变温度为58.9 ℃,导热系数为0.692 W/(m·℃)。由于复合相变材料在此配比下的比热容尚未见报道,本研究采用差式扫描量热仪(耐驰,DSC214)对其固体和液体状态比热容进行测量,分别为1.95 J/(g·K) (30 ℃,固态)和3.07 J/(g·K) (70 ℃,液态)。
图1(b)为填充床三维示意图。图1(c)为填充床结构示意图。填充床内部几何形状为长方体,床体内部长为455 mm,宽为390 mm,高为683.5 mm,相变单元以水平顺排的方式堆积在填充床内部,相变单元行数和列数均为13,单元堆积体的上部及底部均布置多孔板。上部接口(储热进口/释热出口)和底部接口(储热出口/释热进口)布置在水箱侧面(同侧)。本研究采用橡塑保温材料[0.043~0.056 W/m·℃)]对储热装置及工作管路进行保温,填充床保温层厚度为42 mm,工作管路保温层厚度为20 mm。
1.2 实验系统
图2为中低温储热实验台系统图与实物图。中低温储热实验台系统主要组成部分包括:储热填充床、板式换热器1、板式换热器2、管道加热器、水泵、测控系统、热水箱、冷水箱、备用水箱。实验分为储热过程和释热过程。储热过程中,储热流体经水泵从顶部入口流入储热填充床。释热过程中,释热流体经水泵从底部流入储热填充床。实验采用数据采集仪器(National Instruments)配合热电偶(Omega,T型热电偶)实时获取水箱内部温度状况,采用2个PT100热电阻(测温精度:0.1 ℃)获取储热装置进出口温度,采用涡轮流量计(北京格乐普高新技术有限公司,LW-10Z1A1WNSR,不确定度1%)实时获取水箱入口体积流量。
图2 水合盐相变储热装置实验系统图与实物图:(a) 储热装置实验系统图;(b) 储热装置实验实物图
图3(a)为储热装置内部温度测点布置的整体情况,测点分别布置在上部接口(测点名称:Tf,up)、下部接口(测点名称:Tf,down)、相变单元内部(5个,测点名称:Tp1、Tp2、Tp3、Tp4、Tp5)以及流体区域(5个,测点名称:Tf1、Tf2、Tf3、Tf4、Tf5)。内部含温度测点的相变单元位置为第7列(中心列)的1、4、7、10、13行。图3(b)为封装单元内部热电偶布置情况的示意图,热电偶温度测点位于相变单元的几何中心。图3(c)为流体区域内温度测点布置情况示意图,流体区域内温度测点与相变单元内温度测点位于同一径向平面(以相变单元为轴),位于菱形孔隙的几何中心处。
图3 储热装置储/释热试验温度测点布置示意图:(a) 填充床内温度测点布置整体情况;(b) 相变单元内温度测点位置示意图;(c) 流体区域内温度测点位置示意图
1.3 实验步骤
下面首先介绍一次完整储热/释热实验的实验流程。床体初始温度为T1 ℃,蓄热过程装置上部流入的储热流体温度为T2 ℃,释热过程装置底部流入的释热流体温度为T3 ℃(本研究中释热流体与床体初始温度相同,T1=T3):
(1)实验前期准备:利用循环系统及管道加热器,将热水箱内水温加热至约T2-5 ℃。设置加热器出口温度为T3 ℃,利用泵将水从冷水箱抽出,通过加热器将水温控制在T3 ℃,进入储热装置以实现储热装置均温初始化。冷水从储热装置排出后与板式换热器换热,温度降至约T3-3 ℃返回冷水箱。(换热流体工作路径:①—③—④—⑨—⑦—⑧。)
(2)储热实验:储热流体(热水)从热水箱流出,经泵、管道加热器(加热器控温在T2 ℃),从水箱上部入口进入储热装置,以实现储热装置的热量存储。随后,储热流体从水箱底部流出,返回热水箱。(储热流体工作路径:②—③—⑥—⑦—⑨—⑤。)
(3)释热过程:释热流体(冷水)从冷水箱流出,经泵、管道加热器(加热器控温在T3 ℃),从水箱底部入口进入储热装置,以实现储热装置的热量释放。随后,释热流体从水箱顶部流出,经过板式换热器降温后,返回冷水箱。(释热流体工作路径:①—③—④—⑨—⑦—⑧。)
为了研究储热温度和流量对填充床储释热表现的影响,本文设置了储热温度为60 ℃、65 ℃和70 ℃的3种工况(流量为16 L/min,床体初始温度为30 ℃)。辐射式供暖以4口分水器为主,配合12 mm内径加热管,加热管内推荐流速为0.25~0.6 m/s,供水总流量范围在7 L/min至16.28 L/min之间,因此本研究设置了流量为8 L/min、12 L/min和16 L/min的3种工况(床体初始温度为30 ℃,储热温度为70 ℃)。本研究对比了不同工况下填充床储热过程和释热过程的出口温度表现,并通过比较储热过程充入热量、释热过程释放热量、热效率以及储热密度完成对不同工况下填充床储热表现的评估。
参考文献[10],定义量纲为1截止温度DTC*和DTD*如式(1)和式(2)所示:
式(1)和式(2)中,Tcharge为储热过程入口温度;Tdischarge为释热过程入口温度(床体初始温度);Tp1为最顶层单元内测点温度;Tp5为最底层单元内测点温度。为保证储热装置储/释热过程完整,DTC*和DTD*设置为0.99。以床体初始温度30 ℃,储热温度为70 ℃为例,储热过程中,Tp5达到69.6 ℃时,储热过程结束。
各指标的计算方法如下所示:
2 结果与讨论
本节首先对储/释热过程中填充床内部温度演化情况进行讨论,而后研究了储热温度和运行流量对储热装置整体性能的影响。
2.1 填充床内部温度演化规律
在初始温度30 ℃、储热流体70 ℃、流量12 L/min的实验工况下,对填充床内部相变单元及流体区域温度演变情况进行了分析讨论。图 4展示了不同高度处相变单元在储热/释热过程中温度变化情况。图4(a)为储热过程中不同高度处相变单元的温度表现,相变单元在升温过程中温度表现可分为3个阶段:固体显热吸热主导的升温阶段,固液转变主导的恒温阶段(熔化-相变)和液体显热吸热升温阶段。从图4(a)可以看出,位置较高的相变单元率先完成了固-液转变。这是因为储热过程中,储热流体自上而下流动,位置较高的相变单元优先与储热流体换热,且此位置储热流体温度较高。因此,较高位置的相变单元能够更快完成固-液转变。图4(b)为释热过程中,不同高度处相变单元的温度表现,相变单元在降温过程中温度表现可分为3个阶段:液体显热吸热主导的升温阶段,固液转变主导的恒温阶段和固体显热释热阶段。从图4(b)可以看出,位置较低的相变单元在较短时间内完成凝固过程。这是因为释热过程中,取热流体自下而上流动,位置较低的相变单元优先与取热流体换热,且此处位置释热流体温度较低。因此,较低位置的相变单元能够更快完成凝固过程。
图4 竖直方向相变单元储/释热过程中温度变化情况(12 L/min):(a) 储热过程;(b) 释热过程
图5展示了流体区域内不同高度处在储/释热过程中的温度变化情况。图5(a)为储热过程中不同高度处流体区域的温度表现。从图5(a)可以看出,水箱不同高度处的温度均随储热过程逐渐升高,同一时刻下,测点位置越高温度越高。最顶层温度测点在最短时间内升温至70 ℃附近。最底层温度测点的温度依次经历迅速升温、较快速升温和平缓升温3个阶段。图5(b)为释热过程中不同高度处流体区域温度表现,可以看出水箱不同高度处的温度均随释热过程逐渐降低,同一时刻下,床体内位置越低温度越低。最底层温度测点在最短时间内降温至30 ℃。最顶层温度测点温度走势依次经历迅速降温、较快速降温和平缓降温3个阶段。从图5(a)和(b)可以看出,在储热和释热过程中,测点位置的高低与温度变化的平缓段特征有着密切的关系。具体而言,测点位置越低,在储热过程中的平缓升温段特征越明显;而测点位置越高,在释热过程中的平缓降温段特征越显著。这主要是因为相变材料在凝固和熔化过程中会恒温吸热或放热,流体换热量随横掠单元数增加而增大。除此之外,从图5可以看出,释热过程用时小于储热过程,这是因为相变材料熔点为58.9 ℃,储热过程中,储热流体为70 ℃,流体与相变材料熔化界面换热温差最大为11.1 ℃,释热过程中,取热流体为30 ℃,流体与相变材料凝固界面换热温差最大为28.9 ℃,换热温差越大,热传递效果越好,用时越短。
图5 竖直方向流体区域储/释热过程中温度变化情况(12 L/min):(a) 储热过程;(b) 释热过程
2.2 储热温度对填充床储热性能的影响
图6展示了储热温度分别为60 ℃、65 ℃和70 ℃情况下,填充床储/释热过程出口温度表现,所有工况流速均为16 L/min,床体初始温度均为30 ℃。图6(a)为储热过程中,不同储热温度下,填充床出口温度随时间的变化情况。可以看出,随着储热温度的提升,床体储热用时明显缩短。储热温度为60 ℃、65 ℃和70 ℃的工况,储热用时分别为17648s、8298s和6123s。储热温度从60 ℃增加至65 ℃和70 ℃,储热用时分别减少了53%和65%。当储热温度为60 ℃时,热流体与相变材料固液界面间换热温差较小,因此储热功率较低,用时较长。当储热温度提高后,换热流体与相变温度温差增大,同时强化了内部熔化区域的自然对流,储热进程加快,储热用时缩短。图6(b)为释热过程中,不同床体温度下,填充床出口温度随时间的变化情况。从图中可以看出,随着释热过程发展,不同工况下的填充床的出口温度逐渐接近,并以相近温度完成后续释热过程。3种工况下,储热装置释热用时几乎相同。主要由于释热过程中单元内部自然对流较弱,换热由热传导主导,因此释热用时几乎相同。图7对比了不同入口温度下填充床的储热性能。从图中可以看出,储热装置的储热量、释热量、热效率以及储能密度均随储热温度的升高而上升。随着储热温度升高,热效率从89.69%提高至94.37%,储热密度从58.3 kWh/m3增加至71.77 kWh/m3。可以看出,更高的储热温度得到更高储热量的同时,缩短了储热用时,减少了散热能量损失,因此热效率和储热密度均提高。
图6 不同储热温度下储热装置储/释热过程出口温度表现:(a) 储热过程;(b) 释热过程
图7 储热装置在不同储热温度下的性能
2.3 流量对填充床储热性能的影响
本小节展示了流量为8 L/min、12 L/min和16 L/min情况下填充床储/释热过程出口温度,其中床体初始温度为30 ℃,储热温度为70 ℃。图8(a)为储热过程中,不同流速下,填充床出口温度表现。从图中可以看出,随着流量的增加,填充床储热用时缩短。当流量从8 L/min增加至16 L/min,储热用时从9000 s缩短至6123 s,减少了32%。图8(b)为释热过程中,不同流速下,填充床出口温度表现。从图中可以看出,随着流量的增加,填充床的释热用时从4018 s缩短至3122 s,减少了22%。图9为流量对填充床储热性能的影响。从图中可以看出,储热装置的储热量、释热量、热效率以及储能密度均随流量的增加而增加。3个工况的热效率均高于90%,其中运行流量为16 L/min的工况热效率高达94.73%。3个工况的储热密度均高于68 kWh/m3,其中运行流量为16 L/min的工况储能密度为71.77 kWh/m3。这主要是由于流量增加导致流体与外壁面间换热得到增强,同时耦合内部熔化传热的强化,储释热用时缩短。同时向环境散失的热量减少,提高了热效率和储热密度。
图8 不同流量下储热装置蓄释热过程中出口温度:(a) 储热过程;(b) 释热过程
图9 储热装置在不同流量下的储热表现
3 结 论
本文开展了圆柱体水合盐相变材料封装单元有序堆积形成的相变储热装置的实验研究,研究了流量和储热温度对储热性能的影响。研究结果表明:
(1)本研究获得了储/释热过程中填充床内部温度变化情况。在储热过程中,热流体自上而下流动加热相变单元,单元内相变储热材料沿流动方向依次经历固态显热升温、固液恒温相变和液态显热升温3个阶段,上部单元先于底部单元完成熔化。在释热过程中,冷流体自下而上流动冷却相变单元,沿流动方向依次经历液态显热降温、固液恒温相变和固态显热降温3个阶段,底部单元先于上部单元完成凝固。相变材料在凝固过程中无明显过冷现象,具有较好的相变动力学特性。
(2)提高储热温度和增大流量均可缩短储热时长,同时提升填充床储热装置的热效率及储能密度。当流速为16 L/min,储热温度为70 ℃时(床体初始温度30 ℃),储热装置的热效率可达94.73%,储能密度可达71.77 kWh/m3。
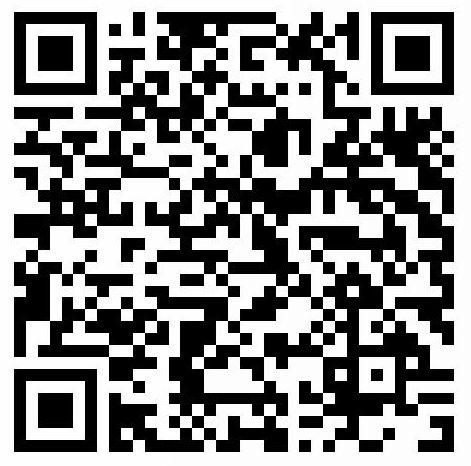
评论